German Ordnung and Japanese Kaizen are at Volga-Dnepr Service!
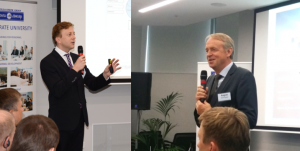
August Henningsen and Johannes Weidisch shared their experience in implementation of LEAN tools in Lufthansa Technik
Another seminar of the CU School for the company executives “Top-class” was conducted in Moscow on September 28. More than 30 participants from Volga-Dnepr offices in Russia, Germany, the UAE gathered to discuss LEAN technologies implementation into aircraft maintenance and repairs.
August Henningsen, the representative of Lufthansa Technik, ex-CEO, a member of the Supervisory Board at present, and his colleague Johannes Weidisch, the acting director of Lean management shared their experience in applying the tools of Lean culture.
The participants’ genuine interest in Lufthansa experience, their active involvement into dialogue contributed much to the seminar efficiency. What the participants valued most was the Q&A session where they learned how it all had started in Lufthansa, resources and expenses involved, mandatory training done and many others.
The teamwork was inspired by the company president Alexey Isaykin:
– There aren’t any everlasting operative decisions. The situation is changing and it requires new approach and decisions. This is what both Lufthansa and Volga-Dnepr always have to learn.
This is what the participants shared:
Ildar Ilyasov, AMTES GmbH managing director:
– The seminar was very practical! It was important that the presentations were made by real professionals with impressive experience in aircraft maintenance and repairs. We have to apply these things in our company. The question I asked was about maintenance process optimization and I got the answer along with solid evidence and examples. We plan our future cooperation with them to learn from each other. This is what we will really benefit from!
Victor Sherin, VD Gulf managing director:
– I really appreciate those five LEAN principles presented by August and Johannes – the examples they gave showed that the technology allowed cutting expenses to 20-30%. Though, we must admit that they had been improving the operative system. For us it is more difficult – we are only on the point of creating it.
Andrey Dyatlov, quality management director, ABC:
– I saw another approach to LEAN technology – that is Lufthansa’s perspective. Their LEAN principles reflect their management system, their mentality, their culture. It was worth learning. People of different age, background, level of responsibility – but all them speak the same values, objectives, approaches to the improvement of their company operation. They do not overlap or interrupt each other. The complement each other, and this is what proves that corporate culture defines a lot. And it’s great that people from different companies of the Group share this value.